China customizable pallet racking system manufacturer
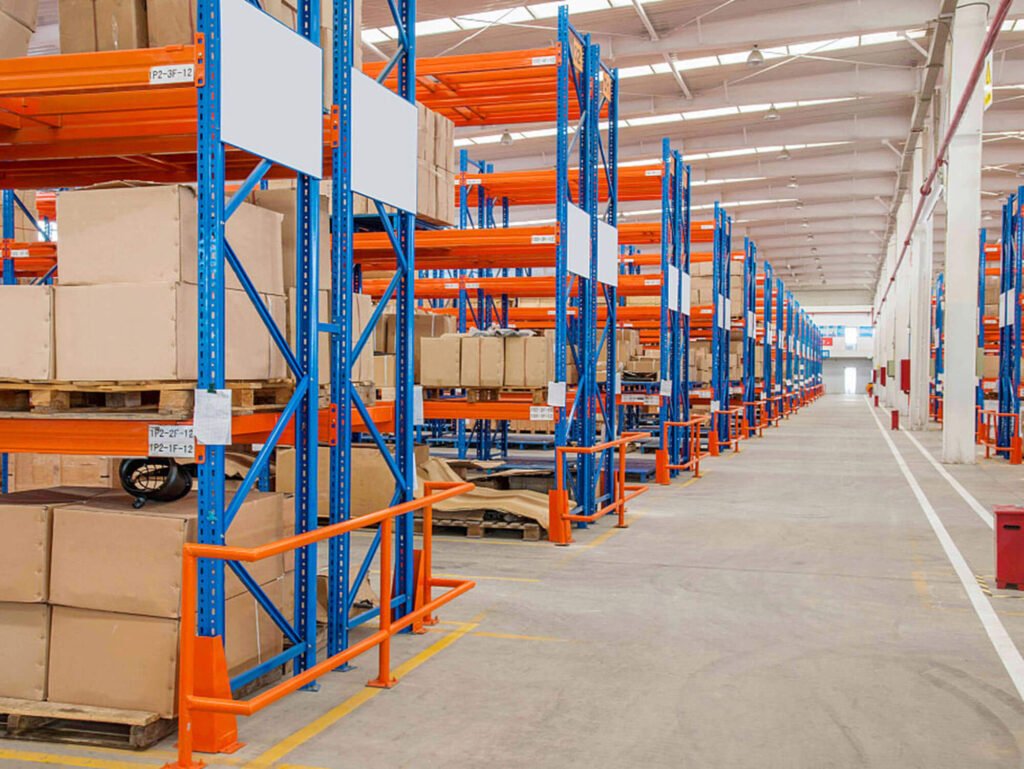
pallet racking system definition
A pallet racking system is a storage solution used to store palletized goods in industrial warehouses or distribution centers. It consists of a combination of upright frames, horizontal beams and other support components that are used to move pallets and goods from the floor to the horizontal beams via forklift trucks for safe and efficient storage and retrieval. The pallet racking system is designed to maximize the use of floor space through the effective use of vertical space. There are many types of pallet racking, including selective pallet racking, drive-in pallet racking, shuttle pallet racking, double-deep pallet racking, and very narrow aisle pallet racking. Different types of pallet racking have their own advantages and limitations, and we need to choose the right pallet racking according to the actual storage needs.
Types of Pallet Racking Systems
The Selective Pallet Racking System is a storage solution designed for traditional warehouses with direct access to each pallet location, allowing easy retrieval of individual pallets without having to move other pallets. It consists of vertical upright frames that support horizontal beams to create a horizontal surface where pallets can be stored. This type of pallet racking is easy to design and is selective, so it is called selective pallet racking.
The teardrop pallet racking system is a type of pallet racking that is widely popular in the Americas and is known for its efficiency and ease of assembly. It features a teardrop shaped hole pattern in the upright frame that allows for quick and secure placement of beams without the need for nuts and bolts. This design is versatile and easy to reconfigure, making it widely used in warehouses to store palletized goods.
Drive-in drive-through pallet racking systems are designed for high-density storage, where pallets are stored in deep aisles and forklifts drive directly into the racking structure to access the pallets. This system eliminates the need for aisles between racks, thus maximizing storage space at the expense of direct access to individual pallets. Drive-in drive-through pallet racking pallet racking is suitable for storing large quantities of similar items using a last-in-first-out (LIFO) inventory management method.
A radio shuttle pallet racking system is an automated storage solution where a shuttle device moves independently along the racks, transporting pallets to and from the loading and unloading positions. It allows for high-density storage with fewer aisles, as the shuttle can efficiently handle pallet movements within the racking structure. This system is suitable for warehouses requiring efficient pallet retrieval and storage, especially in environments with a high volume of pallet handling.
A double deep pallet racking system is a storage solution that stores pallets in two deep rows for higher storage density than traditional selective racking. It is typically designed with deeper pallet storage locations and requires access to the load by a double-deep forklift with greater reach. The system is suitable for warehouses that require increased storage capacity but do not require easy retrieval of individual pallets.
A narrow aisle (VNA) pallet racking system is a high-density storage solution that minimizes aisle widths to maximize storage space. It typically consists of high, dense racking designed to work with specialized narrow aisle forklifts capable of maneuvering through tight spaces.VNA systems make efficient use of vertical space and are suitable for warehouses where space optimization is critical and selective access to individual pallets is required.
An Automated Storage and Retrieval System (AS/RS) is an advanced warehouse solution that utilizes automated machinery, high bay racking and computer systems to efficiently handle the storage, retrieval and movement of goods within a facility. It typically involves the use of robotic cranes, conveyors, and computer controls to automate the handling of pallets, cartons, or individual items.AS/RS maximizes storage efficiency, effectively reduces labor requirements, and optimizes space utilization in the warehouse or distribution center.
The Mobile Pallet Racking System is a dynamic storage solution where the racks are mounted on motorized mobile bases that move along tracks set on the floor. This design eliminates the need for fixed aisles and allows shelves to be compactly located close together to form a high-density storage system. Mobile pallet racking is suitable for warehouses with limited space to maximize storage capacity while maintaining accessibility to stored items.
Factors to Consider When Choosing a Pallet Racking System
There are several factors to consider when choosing the right pallet racking system for your warehouse to ensure that the racking system will meet specific storage needs. The following are key factors to consider when selecting a pallet racking system:
1. type of pallet racking: choose the type of pallet racking that best suits your storage needs. Common types of pallet racking include selective pallet racking, drive-in racking, shuttle pallet racking, double deep pallet racking and very narrow aisle pallet racking.
2. Storage Density: Consider the required storage density based on the amount and type of goods you need to store. High-density racking systems such as drive-in pallet racking are suitable for storing large quantities of goods, while selective pallet racking facilitates access to individual pallets.
3. Product Characteristics: Consider the characteristics of the products to be stored, such as size, weight and perishability. Ensure that the chosen racking system meets the actual requirements of the inventory.
4. Accessibility: Selective pallet racking provides direct access to each pallet, whereas other systems (such as drive-in racking) provide high-density storage but do not provide direct access to each pallet.
5. Inventory management method (FIFO or LIFO): Determine the preferred inventory management method, whether you need to choose First In First Out (FIFO) or Last In First Out (LIFO), different pallet racking systems use different inventory management methods.
6. Ceiling height: Consider the height of the ceiling of the warehouse and the available vertical space. Select a pallet racking system that maximizes vertical storage space while adhering to building height restrictions.
7. Forklift and handling equipment: Ensure that the racking system selected matches the type of forklift and handling equipment used in the warehouse. For example, double-deep pallet racking requires double-deep forklifts.
8. Load capacity: Determine the required load capacity of the pallet racking system based on the weight of the pallets and goods to be stored. Ensure that the pallet racking system is capable of handling the expected loads. 9.
9. Cost: Evaluate the total cost of the pallet racking system, including installation, maintenance and any other accessories required.
10. Compliance: Ensure that the selected pallet racking system complies with relevant local safety regulations and building codes.
By carefully considering these factors, warehouse managers can make an informed decision when selecting a pallet racking system that meets their specific storage needs.
Installation and maintenance of pallet racking systems
The installation of a pallet racking system is a detailed process that involves multiple steps to ensure that the system is assembled properly and safely. This typically includes site assessment, design planning, permitting and compliance inspections, preparation of the installation area, assembly of components such as upright frames and horizontal beams, installation of safety measures, employee training, and documentation of the installation process. Professional support from an experienced installer or following the manufacturer’s guidelines is critical to ensure the stability, safety, and efficiency of your pallet racking system.
Pallet racking system maintenance is critical to ensuring the continued safety, efficiency and functionality of your warehousing infrastructure. Regular maintenance tasks include inspecting for damage, checking load-bearing capacity, tightening bolts and connections, and addressing any signs of wear or corrosion. Implementing a proactive maintenance program can help prevent accidents, protect inventory, and extend the life of your pallet racking system, thereby improving the overall efficiency of your warehouse operations.