China customizable warehouse racking system manufacturer
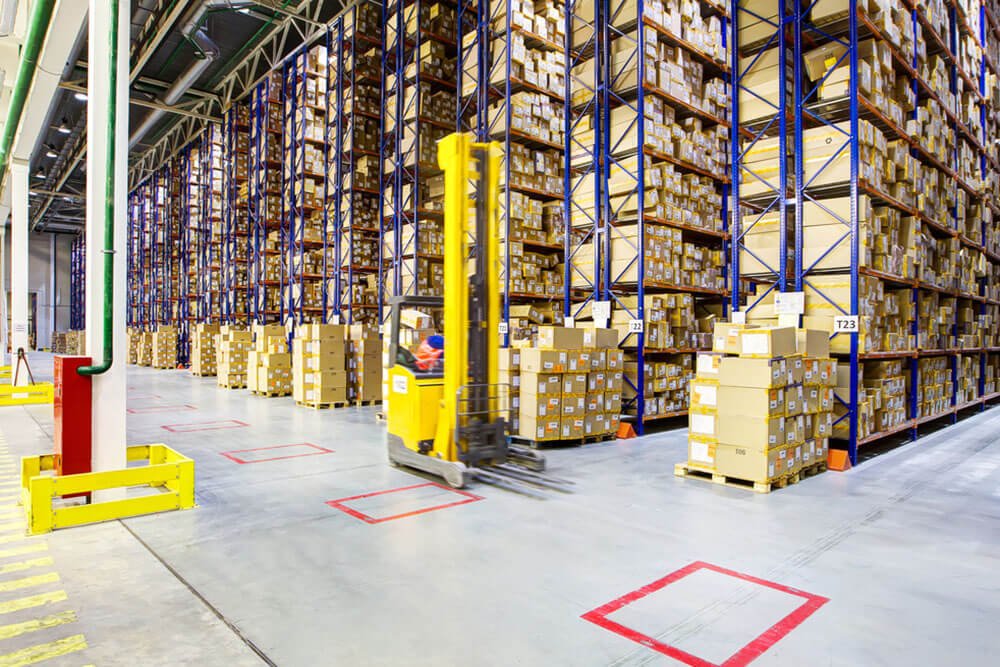
Warehouse racking system definition
A warehouse racking system is a three-dimensional structure that provides safe, organized and efficient storage for all types of goods in a warehouse. Warehouse racking systems consist of various types of warehouse racking designed to stack items vertically to increase storage capacity while making it easy for warehouse personnel to access goods. There are many types of warehouse racking systems, including warehouse pallet racking systems, warehouse cantilever racking systems, warehouse mold racking systems, warehouse stacking racking systems, and more. These racking systems are usually customized based on the size of the warehouse and the actual storage needs. The use of warehouse racking systems helps to maximize warehouse space, reduce handling time, improve inventory control and increase safety within the warehouse.
Types of Warehouse Racking Systems
A pallet racking system is a racking system designed to store palletized goods and is also the most widely used warehouse racking system. When using a pallet racking system, we need to neatly palletize the goods and then access the palletized goods via forklift. Pallet racking system has two different ways of inventory management, namely FIFO and LIFO, you need to choose reasonably according to the characteristics of your stored goods.
The most common pallet racking system in warehouses
Selective pallet racking is the most common type of racking, cheap and easy to install.
Teardrop pallet racking is named for the inverted teardrop-shaped holes in the upright frame.
Drive-in racking is suitable for storing goods with low SKA but high quantities.
Shuttle pallet racking is a type of semi-automated storage racking that is handled by a shuttle truck.
Very narrow aisle racking has very narrow aisles and needs to be coupled with a narrow aisle forklift for storage.
Double-deep rack allows two pallets to be stored at deep in the racking system, and accessed with a double-deep forklift.
The automatic storage and retrieval system is an intelligent racking system controlled by a computer.
Mobile pallet racking requires rails to be installed on the floor, and the entire row of racking is moved when accessing goods.
Cantilever racking systems are warehouse racking systems designed to store lumber, tubing, or other irregularly shaped items. The distinguishing feature of cantilever racking is that there are no front columns on the storage levels and horizontal arms extend outward from the upright columns to provide support for the stored items. According to the type can be divided into single-sided cantilever racking and double-sided cantilever racking, according to the load-bearing capacity can be divided into light-duty cantilever racking and heavy-duty cantilever racking.
Mold racking systems are rack storage systems designed specifically for storing a variety of production molds such as die-casting molds, hardware molds, and injection molds. Mold racks are designed to withstand the tremendous weight of molds, and load-bearing capacity is a key factor in ensuring the safe storage of molds. Our common mold racks have a load capacity of 1000 to 3000kg per level. Mold racks are usually equipped with a crane on the top, which is usually used to access the molds.
Stacking rack is a device derived from pallets for handling and storing goods and can usually be stacked 3 to 5 levels. It can be used as a transfer trolley by adding casters, or folded for space-saving storage. Stacking rack systems can be used in a variety of industries and for different types of goods, from palletized goods to individual products, and they can be adapted to the specific needs of the items to be stored. Its simple structure, low cost and ease of use make it an indispensable piece of equipment for storing and transferring goods.
Factors to Consider When Choosing a Warehouse Racking System
There are several considerations to keep in mind when choosing a warehouse racking system. One of the most important is the need to measure the weight and size of the items to be stored. If the goods are heavy, you will need a warehouse racking system that can handle their weight, such as industrial pallet racking or drive-in racking. Another factor is the available space in the warehouse. You need to choose a racking system that makes perfect use of the available space in the warehouse.
The characteristics of the items themselves are also important factors to consider when choosing a racking system for your warehouse. If the items are perishable, you need to consider the potential impact of the environment on their condition. If the inventory turnover is high, then you can choose a racking system with a FIFO approach to inventory management, such as a selective pallet racking system or a shuttle pallet racking system.
The ease of use of the racking system as well as the maintenance and repair requirements should also be considered. For complex warehouse racking systems such as shuttle racking or ASRS, operators should be professionally trained to work on the system. Correctly selecting the right warehouse racking system can improve operational efficiency, reduce labor costs, and increase storage capacity, thereby improving operating profits.
Installation and maintenance of warehouse racking systems
Correct installation of a warehouse racking system is essential to increase the life and durability of the racking system by ensuring that components are correctly assembled and secured; correctly installing a racking system can resolve potential legal and regulatory issues and reduce the risk of fines or penalties; maximizing warehouse space can be achieved by installing racking in an organized and efficient manner; and correctly installing racking can also help to prevent the risk of rack collapse To ensure the safety of warehouse personnel, rack collapse can lead to serious injury or death, and properly installed racking systems are designed to withstand specific loads and forces, reducing the likelihood of accidents.
Warehouse racking system maintenance is critical to ensuring the continued safety, efficiency and effectiveness of your warehousing infrastructure. With prolonged use, racking is often prone to wear, tear and other forms of damage that can compromise its structural integrity. Developing a racking system maintenance program and performing regular racking system maintenance can help resolve potential problems, prevent accidents and extend the life of your racking system. Regular maintenance of warehouse racking systems is critical to ensure that they function optimally and comply with safety standards, building codes and industry regulations.