Choosing a suitable warehouse storage solution is an important first step in designing a well-organized and efficient inventory facility. A careless selection can negatively influence your budget and hurt your warehouse space utilization.
Therefore, it’s imperative to familiarize yourself with the various categories of warehouse storage solutions available in today’s market. This will definitely ensure that you pick one that fits your facility layout and provides the flexibility you need.
In this article, you will first learn what exactly warehouse storage systems are and explore the most prevalent options to consider for your facility, ranging from manual systems to advanced robotic and automated solutions. There’s also a guide at the end to help you make the correct selection more effectively.
Warehouse Storage Solutions: What Exactly Are They?
Warehouse storage solutions are systems that help in storing and organizing products within a premise. They offer the opportunity to maximize inventory areas, enhance goods tracking, improve accessibility to stored products, and streamline material handling processes.
There are various storage solutions that can satisfy your diverse inventory demands. This article will go over the 12 most prevalent systems favored by many businesses, with the first six being traditional types and the last six being automated solutions.
Top 6 Traditional Warehouse Storage Solutions
Although the following systems are manual, they can be very reliable partners in many cases. Let’s explore the top six traditional warehouse storage solutions available on the market nowadays.
#1: Static Shelving
Static shelving consists of horizontal shelves held up by upright posts. Normally made of Q235B cold-rolled steel, these shelves are the way to go for storing small products (such as documents) that need to be handled by hand since these systems are incompatible with forklifts and other material handling equipment.
Thanks to its affordability and potential to maximize warehouse storage areas, static shelving is widely used by many businesses favoring simplicity and versatility. Typically, they are designed to store relatively light goods, with each shelf holding about 100 to 200 kg.
PROS:
- Capable of supporting relatively large weight loads without cracking.
- Easy for warehouse personnel to install and adjust the shelves.
- Allowing for diverse arrangements, such as U-shaped cells or longer, shorter aisles.
CONS:
- Requiring a large floor space for setup.
- Not very portable.
#2: Mobile Shelving
Like static shelving, mobile shelving is an adaptable storage option for holding your manually picked products. However, by mounting standard shelves on motorized rails or tracks set up on the warehouse floor, mobile shelving (or high-density shelving) facilitates easy movements and removes the need for fixed aisles.
Fewer fixed aisles enable you to free up as much as half of your floor space with mobile shelving, which you can then put to better use by storing more items or giving your staff more space to maneuver.
Level rails, which can be mechanized or operated manually, are a common component of mobile shelving systems. In addition, some of the systems even have locking mechanisms that you can use to restrict who may access your items.
PROS:
- Improving warehouse space utilization.
- Allowing for easier categorization to store a multitude of products.
- Easily altering spacing between layers to fulfill various storage needs.
CONS:
- Demanding strict compliance with safety regulations.
- High investment capital.
#3: Pallet Racking
Pallet racking systems are often considered the backbone of warehouse operations, especially in large facilities. Typically constructed of wood, plastic, or metal, this inventory solution houses heavy loads that are organized on large platforms called pallets via the use of forklifts or other automated systems.
With robust support from upright frames and horizontal beams, it is widely utilized in large-scale, high-throughput processes. In addition to being a great way to optimize vertical space, this system enables dense storage by securely storing pallets in rows over many levels, which in turn reduces unused or wasteful space.
PROS:
- High degree of customization to fit your precise specifications.
- Easy for scalability.
- Making the most of vertical areas for warehouse space optimization.
- Affordable warehouse storage solution.
- Increasing warehouse safety and product accessibility
CONS:
- Lowering a bit of warehouse density.
- Requiring material handling equipment to load and unload pallets.
#4: Carton Flow Racking
As the name suggests, carton flow racking refers to a specific racking system designed to hold items at the carton level. Thanks to a slight incline in the structure, when a carton is removed from the rack, this racking option allows the following carton to glide forward smoothly to cover the space left by that front carton.
When dealing with commodities that move quickly or when a FIFO inventory management approach is crucial, carton flow racks are the way to go. Their strengths lie in environments that handle a large number of small-sized items. They also reduce labor expenses by allowing more picks each hour.
PROS:
- Durable and able to withstand large weights of goods.
- Reducing labor costs and effort.
- Accommodating various SKU sizes.
CONS:
- Relatively high maintenance cost.
#5: Wire Partitions
Warehouses often employ wire partitions as a means of protecting important merchandise as well as establishing temporary work areas. These security-oriented options are easy to set up and take down as they comprise welded and interwoven wire mesh.
For commodities that need more shielding than just a shelf can provide, wire partitions are a wonderful choice. They are ideal for housing large-sized or unusually shaped items, such as balls and tires. However, extremely fragile goods may not go well with wire partitions.
PROS:
- Providing a secure barrier to protect valuable items from theft and unauthorized access.
- Offering great visibility into the enclosed area, where products are stored.
- Highly customizable to fit specific arrangements and storage needs.
- Allowing good air circulation.
CONS:
- Having limited insulation, which is not suitable for temperature-sensitive items.
- Relatively less aesthetically pleasing.
#6: Mezzanine Flooring
While wire partitions focus more on simplicity, mezzanine flooring is the exact opposite, being a more technologically advanced solution. In essence, this warehouse storage system includes extra durable stories built between the facility’s ground level and ceiling.
Often made of wood or concrete and reinforced by steel uprights, mezzanines are a great way to save space and maximize efficiency in a warehouse. They also offer the greatest possibilities for customized features like conveyors, lift systems, and lighting.
Yet, mezzanine floorings are quite costly and may be difficult to implement due to their invasive nature. But compared to building new warehouses, this storage solution is typically less cost-intensive while still allowing you to tap into those unused vertical areas.
PROS:
- More cost-effective than warehouse relocation.
- Effectively enhancing storage space with the additional inventory level.
- Highly customizable to meet specific storage and operational needs.
- Versatile and adaptable to evolving warehouse requirements.
CONS:
- High upfront cost for installation.
- Requiring compliance with building codes and regulations.
Top 6 Automated Warehouse Storage Solutions
If you want to utilize more advanced technology to aid your warehouse operations, let’s give the following six automated storage solutions a chance. These inventory systems don’t rely on manual labor but focus more on automation to ensure top-notch efficiency.
#7: Pick Modules
By integrating conventional storage systems, conveyor belts, and multi-level structures, pick modules are able to optimize your warehouse’s vertical space, picking efficiency, and product flows.
As they can efficiently pick products from multiple spots and consolidate them into a single location, pick modules are most effective in facilities that require pallet assembly of a multitude of SKUs.
PROS:
- Enhancing order picking efficiency by consolidating storage, picking, and sorting activities into a streamlined system.
- Easy for expansion or reconfiguration based on changing storage requirements.
- Reducing errors and improving customer satisfaction with higher order accuracy.
- Making efficient use of warehouse space by combining various storage solutions in a coordinated manner.
CONS:
- Operating pick modules can be complicated, requiring careful training.
- High investment expenses.
#8: Horizontal Carousels
In situations requiring the storage of small, unorganized products or components, horizontal carousels can be an advantageous addition to your facility. Instead of navigating to the product locations, this warehouse storage option is an effective “goods-to-person” system, specifically engineered to accommodate lightweight and compact items.
It functions by utilizing movable horizontal or vertical platforms, which maximize warehouse space utilization and improve operational efficiency. These horizontal carousels provide an exceptional method for preserving a vast assortment of distinct components in a confined area.
There are many horizontal carousel configurations you can install in your facility, depending on your stored items’ sizes and shapes. Typically, horizontal carousels are operated in groupings of two or three units and can retrieve between 150 and 250 items per hour.
PROS:
- Maximizing storage space on a minimal footprint.
- Efficient picking as products are brought to warehouse staff faster.
- Highly flexible, it can handle just about any storage item.
- Increasing warehouse productivity significantly.
CONS:
- Slightly slowing down operations as only one operator can access the carousel at a time.
- Requiring a constant power supply to function.
#9: Automated Storage & Retrieval System (AS/RS)
Unlike traditional warehouse storage solutions, Automated Storage and Retrieval Systems, or AS/RS, optimize pallet storage space and picking accuracy by automating the process of storing and retrieving products via computers and shuttles.
Therefore, this novel storage solution eliminates human error and its associated problems, such as wrong inventory counts, mispicks, and misplaced goods. Moreover, AS/RS allows for ultra-high-density storage, as shuttles and other related robots require less space to handle items.
The systems can be implemented in existing warehouses as a stand-alone module, or surrounded by new facilities meticulously tailored to them. Ideal candidates for AS/RS include facilities managing a substantial quantity of products that require long inventory durations, as well as those aiming to optimize their usable storage space.
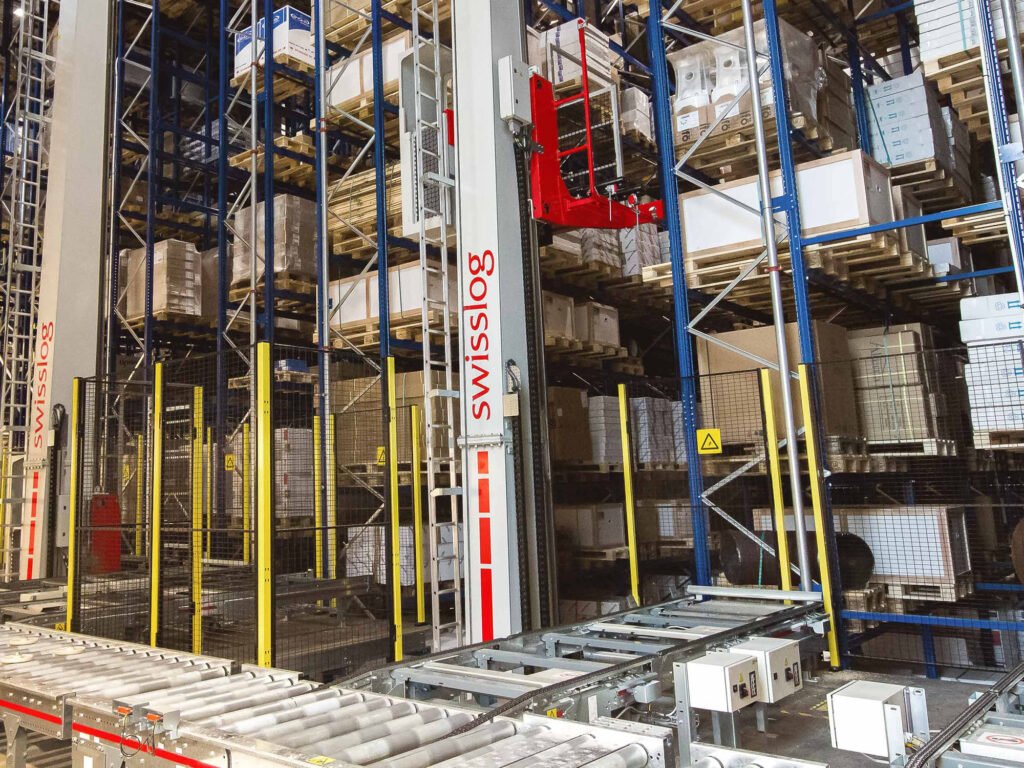
PROS:
- Increasing storage capacity vertically.
- Enhancing workplace efficiency with higher throughput and accuracy.
- Reducing safety risks by replacing workers with machines.
- Automating various warehouse tasks, freeing up workers for more productive functions.
CONS:
- Difficult to customize once integrated.
- Potentially facing load imbalances
#10: Vertical Lift Modules (VLMs)
Vertical Lift Modules are a typical AS/RS type that uses extraction devices placed between two rows of stored products. The function of these vertically arranged trays is to retrieve the desired objects and deliver them to a designated spot at the end of the module whenever a request is made.
With VLMs, you may improve your warehouse storage capacity and save labor expenses via automated procedures, eventually leading to maximizing the usage of vertical storage space.
This warehouse storage mechanism shines in facilities that deal with a diverse variety of SKUs. It is also a great option for warehouses that want to save time and effort by storing and retrieving items more efficiently.
Typically, as a picking module, VLMs are often set up in pairs or trios, with the capability of getting 250 to 350 picks each hour from a single operator.
PROS:
- Optimizing warehouse space with a space-saving design.
- Allowing for multi-user access at the same time.
- High versatility with application across various industries.
- Boosting productivity and workplace efficiency via automation.
CONS:
- High initial costs (like other automated warehouse storage solutions).
- Needing regular maintenance to run smoothly.
#11: Autonomous Mobile Robots (AMRs)
Thanks to autonomous mobile robots (AMRs), no more costly and time-consuming remodeling of your facility is required. These storage solutions are a revolutionary new way to store and retrieve items with increased flexibility.
Basically, AMRs are robots that can independently select and store products within your facility. With the help of built-in cameras and warehouse management software, they can pinpoint exactly where the required products are located and find the optimal way to reach them.
If your organization is looking to automate labor activities without undergoing major renovations, AMRs are a brilliant choice to consider. Not only are these technological marvels versatile for improving warehouse operations, but they are also compatible with a variety of conventional storage solutions.
PROS:
- Planning optimal paths to a given destination with no need for guiding infrastructure such as magnetic tapes.
- Quickly adapting to equipment and personnel moving around the facility.
- Able to handle new routes, new warehouses, and new workflows without the need for robotics experts’ intervention.
CONS:
- Moving relatively slowly and requiring to be charged.
- Slightly limited load capacity.
#12: Pick-To-Light (Put-To-Light) Systems
In comparison to other automated storage systems, pick-to-light (or put-to-light) options have a much lower hardware and installation cost. They are useful for distribution facilities that use team-based order fulfillment methods (such as zone picking) or warehouses with high-density and fast-moving products.
Instead of reading the order manually, which is time-consuming, pickers can rely on barcode scanning to navigate the exact position of an SKU. In front of each SKU’s pick face, there is an illuminated display showing the amount the pickers need to select or deposit.
PROS:
- Offering a paperless picking process with high order fulfillment precision.
- Easy to use for pickers with less training.
- Strengthening many management control functions.
CONS:
- Performing well only when picks are small and the picking area is near.
- Being prone to hacking due to the solution’s wireless system.
Why Having Suitable Warehouse Storage Solutions Is Important
The key to a successful warehouse is to have an efficient storage system. In this part, let’s explore why owning a suitable warehouse storage solution is crucial for your warehouse.
- Increasing workplace safety: Your warehouse’s safety, including the well-being of your staff, goods, and machinery, is of the utmost importance. Storage solutions facilitate a clean and well-organized facility, which increases safety for warehouse personnel.
- Maximizing storage space: Investing in contemporary storage systems allows warehouse personnel to optimize the available space for inventory, which is one of the major motivators.
- Enhancing efficiency: With the correct warehouse storage system, your staff will be able to locate products much more quickly and accurately. An effective inventory solution can also enhance your time-to-market capabilities, thanks to the rapid retrieval and efficient goods flow.
- Cost-effective: Improving an already established warehouse solution is often more practical and economical than building a whole new facility from the ground up. A suitable warehouse storage system enables you to keep all products in a well-organized manner at more reasonable prices.
Key Pointers For Selecting Suitable Warehouse Storage Solutions
In order to maximize space utilization and enhance product flows, it is crucial to choose the appropriate warehouse storage solutions for your premises. This part will outline key pointers to help you make the correct decision.
Assessing Your Storage Demands
Before delving into the selection process, you need to have a good grasp of your warehouse storage requirements. Think about things like the size and weight of your stocks. Are you in need of a facility to house bulky boxes? Is it practical to add an additional storage level to the current warehouse?
Moving to a larger premise should always be the last resort when all other options are out of the question. Not only is relocation cost-intensive, but this measure also requires lots of effort in order to find a suitable premise.
Evaluating Your Existing Warehouse
Find out how much storage room there is in your facility, including both vertical space and floor areas. These inputs are valuable in helping you determine the optimal warehouse storage solutions.
For instance, AS/RS may save up to 90% of floor space in situations where floor space is at a premium but ceiling height is abundant.
Analyzing Various Inventory Systems
Finding the best storage solutions for your inventory needs requires evaluating many options. If you’re having a smaller number of SKUs, static shelving works particularly well. However, for a greater number of items, the pallet racking system is more suitable.
But once you plan to make the most of your warehouse’s vertical capacity while saving precious floor space, Automated Storage and Retrieval Systems are once again worth your consideration.
Integrating Technology
To keep tabs on stock levels in real time, think about inventory solutions that can be connected to warehouse management software (WMS). If you want to avoid running out of stock, consider combining a WMS with Automated Storage and Retrieval Systems.
Oftentimes, technology only works with automated warehouse storage solutions as it cannot be integrated with manual options.
Examining Your Available Budget
While advanced storage solutions, such as AS/RS, can be more expensive than traditional mechanisms like pallet racking systems, they pay for themselves in the long run via increased storage density, reduced labor expenses, and more precise picking.
However, if you’re on a tight budget, there are still many brilliant storage solutions that you can consider for your warehouse, mainly manual options.
Conclusion
Evidently, there are a plethora of warehouse storage solutions that you can consider integrating into your facility. You may improve the storage efficiency of your warehouse in a number of ways, some of which are more conventional and others of which are more cutting-edge and automated.
As time goes on, these systems will only get more technologically advanced, lightweight, and reasonably priced. Therefore, you don’t need to stick with inventory systems that don’t work. Instead, try different options to see which solutions suit you the best.
In conclusion, it is critical that you make the correct choice for your facility. Everything from your objectives, premise layout, available floor space, vertical height, throughput needs, and specific inventory characteristics will determine which choice (or choices) is ideal for you.